Das Institut für Umformtechnik an der Universität Stuttgart blickt in der Forschung auf dem Gebiet der Massivumformung und insbesondere in der Kaltmassivumformung auf eine jahrzehntelange Erfahrung zurück. Der wissenschaftliche Schwerpunkt liegt auf dem ganzheitlichen Prozessverständnis, beginnend bei der numerischen Modellierung des Prozessablaufs, dessen Auslegung bis hin zur Versuchsdurchführung und Modellvalidierung. Seit Beginn der Forschungsaktivitäten Ende der fünfziger Jahre im Bereich der Massivumformung stellt die Verfahrensentwicklung neuartiger Kaltfließpressprozesse einen zentralen Bestandteil der Forschungsarbeiten dieser Abteilung dar. Im Vordergrund stehen dabei die Fragestellungen des konstruktiven und stofflichen Leichtbaus, der umformtechnischen Erzeugung von verzahnten Getriebekomponenten, der Digitalisierung und Regelung von Prozessabläufen sowie der Erzeugung von Mehrkomponenten-Verbundbauteilen. Die Erarbeitung neuartiger technologischer Lösungen erfolgt durch die Charakterisierung verfahrensspezifischer Werkstoffeigenschaften und Reibungsbedingungen mithilfe eines breiten Einsatzes numerischer Methoden, experimenteller Validierung sowie durch die Analyse der Betriebseigenschaften kaltumgeformter Bauteile. Neben der Grundlagenforschung werden weiterhin aktuelle praxisorientierte Fragestellungen im Zuge von Industrieprojekten behandelt. Hierbei stehen insbesondere die Verfahrens- und Werkzeugauslegung sowie die experimentelle Erprobung im Versuchsfeld des Institutes im Vordergrund.
Das Kaltfließpressen von Aluminiumlegierungen zählt zu einer kostengünstigen Mengenfertigung präziser Bauteile, die oft einbaufertig hergestellt werden. Aufgrund seiner herausragenden Eigenschaften wie geringe Dichte, hohe Korrosionsbeständigkeit oder der Lebensmittelverträglichkeit, zählt Aluminium neben Stahl zu dem wichtigsten Werkstoff in der Kaltfließpresstechnik. Zudem zeichnen sich Aluminiumlegierungen durch gute Verarbeitungs- und Gebrauchseigenschaf en aus, wie geringer Presskraftbedarf und hoher erreichbarer Umformgrad. Zu den gängigsten Werkstoffen zählt zum Beispiel die Legierung EN AW 6082.
Die weitere Forschung und Entwicklung auf dem Gebiet des Kaltfließpressens von Aluminiumlegierungen ist eine wichtige Voraussetzung für den gezielten Einsatz von Leichtbauprodukten in mobilen Strukturen. Die Ermittlung von Werkstoffkennwerten stellt dabei die Basis für die Simulation von ein- und mehrstufigen Umformprozessen für die Kaltumformung sowie der Umformung bei erhöhten Temperaturen dar. Das tribologische Zusammenwirken zwischen Werkzeug und Werkstoff unter den Einfluss verschiedener Oberflächenschichten bzw. -strukturen wird zum Beispiel anhand des Spiketests, eine Kombination aus Stauchen und Voll-Vorwärts-Fließpressen, untersucht. Zur Ermittlung der optimalen Butzenoberfläche in Verbindung mit verschiedenen Schmierstoffen eignet sich wiederum das Napf-Rückwärts-Fließpressen aufgrund der Oberflächenvergrößerung während des Prozesses.
Mittels gezielter Wärmebehandlung entstehen hochfeste Aluminiumlegierungen, die weiteres Potential bieten, komplexe Leichtbaustrukturen zu fertigen. Die höchsten Festigkeitseigenschaften bietet zum Beispiel der Zustand T6 der durch ein Lösungsglühen und anschließendem Abschrecken sowie einer Warmauslagerung erreicht wird. Bei diesen Werkstoffen richtet sich der Fokus u.a. auf die Ermittlung der Umformeigenschaften verschiedener Legierungen bei erhöhten Temperaturen. In diesem Zusammenhang spielt auch die Mikrostruktur der gepressten Bauteile eine immer größere Rolle, die auf die Erhöhung der Festigkeit während der Umformung bzw. auf die Zerspanungseigenschaften nach der Umformung Einfluss nimmt.
Im Jahr 2010 lag der die Aluminiumproduktion weltweit bei ca. 49,6 Millionen Tonnen. In Zukunft ist mit einer weiteren Zunahme der Aluminiumproduktion sowie von Bauteilen aus hochfesten Legierungen zu rechnen.
Auf der Suche nach Lösungen zur wirtschaftlichen Herstellung von Massivumformteilen von hoher Qualität wird in deutschsprachigen europäischen Ländern der Ansatz verfolgt, Stahl bei Temperaturen bis zu 500°C durch Fließpressen zu verarbeiten. Für die Umformung in diesem Temperaturbereich etablierte sich im deutschsprachigen Raum die Begrifflichkeit „Lauwarmumformung“ in Abgrenzung zur industriellen Halbwarmumformung mit Temperaturen oberhalb von 500°C. Als besonders geeignet erweisen sich Temperaturbereiche unterhalb oder oberhalb der Blausprödigkeit, bei denen sich Stahlwerkstoffe durch eine hohe Duktilität und niedrige Fliessspannungen auszeichnen. Untersuchungen zum Fließpressen im genannten Temperaturbereich, unterteilt in die Arbeitspakte Tribologie, Werkstoffe und Bauteileigenschaften, werden zurzeit am IFU im Arbeitskreis für Entwicklung und Erforschung des Kaltpressens durchgeführt.
Praktiker erhoffen sich durch das Umformen in diesem Temperaturbereich die Herstellbarkeit von Werkstücken mit annähernd gleich bleibender Genauigkeit und Oberflächenqualität wie bei der Kaltumformung, jedoch bei erweiterten Möglichkeiten des Werkstoffspektrums, der Formgebungsmöglichkeiten durch Erhöhung des Umformvermögens und höheren Werkzeugstandzeiten durch niedrigere Prozesskräfte. Gegenüber der konventionellen Kaltmassivumformung lassen sich durch das Erwärmen von Rohteilen vor dem Umformen ebenso zeit- und kostenintensive Oberflächenbehandlungsschritte, Zwischenglühoperationen oder sogar einzelne Umformstufen einsparen.
Getriebewellen weisen aus heutiger Sicht durchaus ein Potenzial hinsichtlich des konstruktiven Leichtbaus auf. An unbelasteten Stellen im Inneren wird gezielt Material eingespart und die Masse dieser gewichtsoptimierten, hohlen Wellen in radialer und axialer Richtung funktionsgerecht platziert.
Für das Herstellen von hohlen Getriebewellen mit fertigbearbeiteten Funktionsflächen hat sich das Kaltfließpressen etabliert. Hohlformen lassen sich durch Napf-Fließpressen und anschließenden Entfernen des Napfbodens herstellen. Weiterhin werden Fließpressverfahren wie Hohlvorwärts- und Hohlrückwärtsfließpressen eingesetzt, die in der industriellen Praxis auch mit anderen Kaltumformverfahren wie z. B. dem Abstreckgleitziehen, Verjüngen (Einhalsen) oder Anstauchen zur Herstellung hohler Bauteilen kombiniert werden. Das Kaltfließpressen bietet als umformtechnisches und spanloses Fertigungsverfahren die Möglichkeit, Formelemente wie Verzahnungen, Flansche oder Lagerschalen an hohlen Bauteilen in einbaufertiger Qualität (net shape oder near net shape) zu erzeugen. Dies erlaubt eine Reduzierung der nachfolgenden Fertigungsschritte, einen geringeren Materialeinsatz und weniger Fertigungskosten bei gleichbleibendem oder erhöhtem Anteil an der Wertschöpfungskette für den Bauteillieferanten.
Die Forschungsaktivitäten am IFU fokussieren in diesem Bereich auf technologischen Entwicklungen von Fließpressverfahren für die Erzeugung hochgenauer kaltgepresster mehrfachverzahnter Getriebewellen und für die Erweiterung von Verfahrensgrenzen beim Anstauchen von Flanschen und Bunden an hohlen Fließpressteilen.
Das Scherschneiden stellt oft den ersten Prozessschritt innerhalb einer mehrstufigen Fertigung von Pressteilen dar. Es ist ein hochproduktives Verfahren und löste das Sägen zur Halbzeugherstellung ab, bei dem die Werkstofftrennung nur durch Materialverlust realisierbar war. Beim Scherschneiden erfolgt die Werkstofftrennung ohne Materialverlust, indem der Werkstoff in der Scherzone zwischen zwei aneinander vorbeibewegten Messern getrennt wird. Das Verfahren Kaltfließpressen verlangt beispielsweise kurze Rohteilabschnitte mit geringen Masseschwankungen sowie ebene Trennflächen, die senkrecht zur Mittelachse sind.
Des Weiteren sollten sie keine Risse, geringe Verformungen und nach Möglichkeit keinen Grat aufweisen. Geringe Geometrietoleranzen können durch einen anschließenden Setzprozess ausgeglichen werden. Die Entwicklungen führten in der letzten Dekade vom konventionellen Scherschneiden zum Hochgeschwindigkeitsscherschneiden bei dem nach Definition Schergeschwindigkeiten von höher als 10m/s erreicht werden. Diese Geschwindigkeit lässt sich oft nur durch einen Impuls erreichen.
Durch die hohen Geschwindigkeiten, kommt zu einem sogenannten adiabatischen Scherband im Werkstoff, in dem die Wärme nicht schnell genug abgeführt werden kann und es zu einer Entfestigung des Werkstoffes kommt. Die Folge sind verbesserte Schnittqualitäten am Halbzeug. Spezifisch sind Schnittflächen, die einen hohen Bruchanteil besitzen. Es wird zwischen Offenschneiden und Geschlossenschneiden unterschieden. Während das Offenschneiden in der Massivumformung vor allem das Trennen von Stangen zu kurzen Abschnitten bezeichnet, wird das Geschlossenschneiden auch als Lochen definiert, bei dem zum Beispiel aus einem Napf ein bodenloser Zylinder entsteht.
Die Kombination der beiden Fertigungsgrundverfahren Umformen und Fügen erlaubt zum einen eine Reduzierung von Fertigungsschritten. Im Vergleich zu einer konventionellen sequentiellen Fertigung kann mindestens die Herstellung eines Fügepartners mit dem Fügeprozess kombiniert werden. Des Weiteren können Toleranzanforderungen bei derartigen Fügeverfahren vernachlässigt werden, da sich in der Regel eine ausreichend hohe Flächenpressung in der Kontaktfläche beider Fügepartner einstellt, welche keinen Spalt zulässt. Neben form- und kraft schlüssigen (bzw. reibschlüssigen) Verbindungen lassen sich durch gemeinsames Fließpressen zweier Halbzeuge bedingt auch stoffschlüssige Verbindungen erzielen. Im Vergleich zu konventionellen Fügeverfahren können auch artverschiedene Werkstoffe ohne thermische Belastung verbunden werden. Die bei der Umformung auftretende elastische Rückfederung der umgeformten Fügepartner kann jedoch zu einem Verlust des Kontaktdruckes und somit einer Minderung der Verbindungsqualität führen.
Daher erfolgt die numerische Prozessauslegung eines Fügeprozesses mittels elastisch-plastischer Deformation in der Regel mit elastisch-plastischen Werkzeugmodellen beider Fügepartner und einem elastischen Werkstoffverhalten der Werkzeugaktivelemente. Neben der Kompensation bzw. Nutzung der elastischen Rückfederung beim Fügen mittels elastischer-plastischer Deformation stellt die Tribologie derartiger Prozesse eine weitere Herausforderung dar. Während des Umformprozesses zur Herstellung form- und kraftschlüssiger Verbindungen sollten möglichst geringe Reibungswerte in der Kontaktfläche auftreten. Das gefügte Bauteil erfordert vor allem bei rein kraftschlüssigen Verbindungen einen hohen Haftungs- und Gleitreibungswert in der Kontaktfläche.
Die kontinuierliche Verbesserung von Fließpressverfahren durch Erweiterung der Verfahrensgrenzen oder die Herstellung komplexer Pressteile erfordert oftmals Verfahrenskombinationen, die darüber hinaus die Anzahl der erforderlichen Umformstufen reduzieren können. Bei der Substitution mehrstufiger Umformverfahren durch einstufige Verfahrenskombinationen ist eine Kontrolle des Materialflusses während des Umformens wünschenswert. Darüber hinaus kann bei der Steuerung des Materialflusses eine flexible Produktion sichergestellt und z.B. auf Chargenschwankungen der Rohteile oder Konstruktionsänderungen flexibel reagiert werden. Die sogenannte Net-Shape Fertigung und Null-Fehler Strategien sind somit in Reichweite.
Die Regelung von Fließpressprozessen kann durch Integration regelbarer zusätzlicher hydraulischer Achsen in Massivumformwerkzeugen erfolgen. Durch eine adaptive Regelung dieser Achsen, können neben der verbesserten Prozesssicherheit konventioneller Verfahren auch neue Umformverfahren entwickelt werden. Die Bereitstellung der erforderlichen Ölvolumenströme und Öldrücke erfolgt durch ein Hydraulikaggregat. Umformpresse, Hydraulikaggregat und Hydraulikachsen sind über eine zentrale Steuerung verbunden mittels derer die zusätzlichen Achsen parametrisiert und die Zielgrößen für die Regelung definiert werden können. Die Ermittlung komplexer Sollkurvenverläufe der zusätzlichen hydraulischen Achsen erfolgt mittels Kopplung von Software für multidisziplinäre Optimierungsansätze und numerischer Simulation des Umformprozesses. Weiterhin ist durch die hydraulischen Werkzeugachsen eine Substitution mechanischer oder gasbetriebener Federn möglich. Darüber hinaus können innerhalb physikalischer Grenzen nahezu beliebige Federkennlinien realisiert werden.
Bei den Verfahren des Quer-Fließpressens handelt es sich um Fließpressverfahren mit einem lateralen Werkstofffluss, wobei ein Rohteil in einem geschlossenen Werkzeug unter der Wirkung eines oder mehrerer Stempel gleichzeitig in eine oder mehrere Richtungen ausgepresst wird. Quer-Fließ-pressen wird bereits seit den 1960er Jahren wissenschaftlich untersucht und seit Ende der 1970er Jahre werden auch in Deutschland Grundsatzuntersuchungen zu diesem Verfahren durchgeführt, vor allem am IFU. Die Verfahren des Quer-Fließpressens ermöglichen die umformtechnische Fertigung von Bauteilen in Near-Net-Shape-Qualität, deren Form durch andere Fließpressverfahren nicht darstellbar ist. Jene Teileklassen, die durch Quer-Fließpressverfahren herstellbar sind, können in rotationssymmetrische, nicht rotationssymmetrische und profilierte Werkstücke unterschieden und des Weiteren nach der Anordnung (in einer Ebene oder in mehreren Ebenen) und Gestaltung (voll oder hohl) der Nebenformelemente eingeteilt werden.
Quer-Fließpresswerkzeuge zur Herstellung von Werkstücken mit seitlichen Formelementen sind stets horizontal oder vertikal geteilt, so dass das Werkstück nach dem Pressvorgang aus dem Werkzeug entnommen werden kann. Die horizontale Teilung hat den Vorteil, dass entweder mehrfach wirkende Pressen die notwendige Werkzeugschließbewegung sowie die Schließ-und Umformkraft erzeugen können oder aber eine Kopplung der Werkzeugschließbewegung mit der Stößelbewegung einfach wirkender Maschinen durch den Einsatz von so genannten Schließvorrichtungen möglich ist. In der Zeit von 1994–2006 wurde sich am IFU intensiv mit der systematischen Entwicklung neuartiger konstruktiver Konzepte für Schließvorrichtungen befasst.
Die Forschungsaktivitäten am IFU wurden im Bereich des Quer-Fließpressens in den letzten Jahren auf Leichtbauthemen fokussiert. Im Mittelpunkt stehen Forschungsarbeiten zur Verarbeitung von Leichtbauwerkstoffen wie Aluminium, Magnesium, Sinterwerkstoffen oder höherfesten Stählen und zur umformtechnischen Herstellung hohler Quer-Fließpressbauteile durch verfahrensspezifische Entwicklungen.
Seit ca. 1950 sind systematische Untersuchungen über die Ultraschallbeeinflussung bestimmter Umformvorgänge bekannt. Grundsätzlich ist es möglich, die Umformwerkzeuge, oder das Umformgut, oder sowohl die Werkzeuge als auch das Umformgut zu erregen. Durch eine Schwingungsbeeinflussung des Umformprozesses lassen sich folgende Effekte erzielen:
-
Reduzierung der Umformkräfte
-
Beeinflussung der Werkstückeigenschaften
Als Ursache für diese Effekte werden vier Hypothesen aufgeführt, deren Bedeutung jedoch noch nicht eindeutig geklärt ist. Zum einen wird aus werkstofflicher Sicht eine zusätzliche Spannungsüberlagerung oder eine Aktivierung ungünstigerer Gleitsysteme als Ursache vermutet. Andererseits scheint aus prozesstechnischer Sicht eine positive Beeinflussung des tribologischen Systems oder aber eine lokale, oberflächennahe Erwärmung infolge der mechanischen Schwingung der Grund für die oben genannten Effekte zu sein.
Zwei wesentliche Aufgaben bei der Beeinflussung von Umformprozessen mittels Ultraschallschwingungen sind zum einen die Werkzeugkonstruktion und zum anderen die Betrachtung des tribologischen Systems. Die zur Werkzeugkonstruktion notwendige Ermittlung einer an die komplexen Schwingungsmodi angepassten Geometrie erfolgt hierbei numerisch mit Hilfe einer Modalanalyse. Dabei ist eine Schwingungsisolation der passiven Werkzeugelemente und der Maschine zu realisieren, wodurch ein Großteil der mechanischen Schwingung in der Umformzone verbleibt. Bei der Betrachtung des tribologischen Systems werden in der Regel Machbarkeitsuntersuchungen in vereinfachtem Maßstab durchgeführt. Hierzu sind am Institut für Umformtechnik verschiedene Ultraschallgeneratoren und Schallwandler vorhanden.
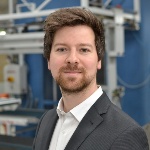
Alexander Weiß
M.Sc.Stellvertretender Abteilungsleiter Massivumformung