The transfer of knowledge, process engineering experience and new technological developments in forming technology into industrial practice is at the forefront of the activities of the UMFORMTECHNIK start-up centre. The initiative to transfer research results often arises due to economic trends in the market for components manufactured using forming technology or due to new materials for products manufactured using forming technology that are currently being launched on the market.
The development and implementation of new methods and processes of sheet metal forming from the ‘laboratory’ into a corresponding production technology in the company is the focus of various development projects of the Transfer and Start-up Centre UMFORMTECHNIK at the Institute of Forming Technology at the University of Stuttgart. The focus here is on the characterisation of new sheet metal materials with regard to their manufacturing limits, their properties at the limits of established sheet metal forming processes, special studies on the topics of simulation, tool and press technology, and much more.
The fields of work of the UMFORMTECHNIK start-up centre at the Institute of Forming Technology range from series and special processes with corresponding measurement, testing and plant technology at the institute, to fundamental investigations, targeted further developments and the optimisation or combination of established processes with new processes (joining, fibre applications, etc.). These include the process development of magnesium sheet metal moulded parts, the production of stainless steel and titanium sheet metal moulded parts at elevated temperatures, as well as the combination of textile-sheet metal composites in conventional forming processes, and much more.
Sheet Metal Forming and Hydroforming
- Conducting Forming Simulations
- Analysis of Shape Changes in Components
- Wear Investigations Under Production Conditions
- Process Questions / Process Optimization / Modification of Forming Tools
- Investigations on Sensitivity, Robustness, and Numerical Optimization of Sheet Metal Forming Processes
- Studies on Energy Consumption During the Forming Process
- Fundamental Investigations on Deep Drawing and Stretch Forming
- Tribological Analyses / Measurements / Surface Topography Mapping of Tools and Blanks / Lubricant Investigations
- Tool Construction: Prototype Tools and Production-Ready Forming Tools / Delivery of Sample Parts Up to 10,000 Components Per Year
- Design of Method Plans for Simple Sheet Metal Parts and Processing of Process-Specific Questions Related to Manufacturability
- Production of Prototype Textile Fiber Sheets, Forming Trials, Characterization of Component Properties, etc.
- Temperature Management in Forming Tools: Cooling and Heating Using Electrical Energy
The energy-efficient and resource-saving use of materials is a key design criterion for future components, assemblies and suitable production systems in today's forging industry. Maintaining technological leadership in this field means meeting the constantly increasing demands on new products in terms of their specific strength, component reliability and other property profiles as economically and resource-efficiently as possible.
In the field of solid forming, the UMFORMTECHNIK start-up centre is therefore working on new types of process control for the production of hollow workpieces by impact extrusion, the redesign of processes for processing higher-strength materials, new types of temperature control before, during and after forming and new control concepts for cold extrusion processes. These completely new developments are intended to provide technological approaches to keep product quality within narrow limits, even close to the process limits.
Bulk Metal Forming
- Investigation of All Currently Known Cold Forging Processes
- Conducting Forming Simulations
- Process Questions / Process Optimization
- Investigations on Sensitivity, Robustness, and Numerical Optimization of Bulk Forming Processes
- Further Development of Cold Bulk Forming Processes
- Feasibility Studies, Including Process Simulation, Tool Design, Tool Commissioning, Parameter Variation, and Production of Sample Parts
- Analysis of Raw Parts and Components (Surface, Microhardness Distribution)
- Failure Analysis and Optimization of Established Cold Forging Processes Using Process Simulation, Optical Methods, etc.
- Recording of Compression Flow Curves with the Thermomechanical Testing System GLEEBLE 3800c
- Tribo-Tests to Evaluate the Suitability of Lubricants or Tool Materials for Conventional Forging Processes, Especially for High-Strength Materials
- Development of Novel Forging Processes Through Process Combinations or Integration of Additional Manufacturing Steps (Interdepartmental Collaboration)
Moulding in the semi-liquid material state and, in particular, thixo-forging refers to the moulding of metallic materials between the solidus and liquidus temperatures of the alloys used. The manufacturing process enables the sophisticated shaping of difficult-to-cast wrought alloys and therefore has a clear advantage over the conventional die casting process. Further advantages of this semi-solid moulding are shorter cycle times, a lower proportion of pores, fewer blowholes and material inclusions, as well as improved mechanical properties, for example in the form of higher strength values and elongation at break compared to various casting processes.
In addition, the components produced can have complex geometries with both thick- and thin-walled shapes as well as long flow paths and achieve excellent surface qualities. The projects in the field of thixo-moulding at TGZ UMFORMTECHNIK relate in particular to applications and component developments for medical technology and the automotive industry. The aim is to develop near-net-shape and net-shape moulding processes for biocompatible and high-melting-point materials from a production-oriented and economic perspective.
Forming Processes (Semi-Solid Forming Technology)
- Rheological Measurements of Metallic Materials in Semi-Liquid States
- Design and Construction of Prototype Tools for Forming in Semi-Liquid Material States
- Adjustment of the Forming Process and Production of Experimental Components
- Thermodynamic Design of Forming Tools (Ansys Workbench)
- Flow Simulation of Material Flow in Forming Tools (Flow-3D)
- Rheological Investigation of Metallic Materials (up to 1000°C; High-Temperature Rheometer)
- Thermomechanical Material Characterization for Forming in Semi-Liquid Material States (GLEEBLE 3800c)
- Examination of Generated Microstructures and Preparation of Corresponding Test Specimens
Knowledge of the forming properties of metallic materials is required to optimise the design of corresponding components and production processes. To determine these properties, the start-up centre has numerous procedures, measuring methods and testing machines at its disposal for characterising sheet materials, bar material, profiles and wires. In addition to the conventional characterisation methods, new testing methods are used that enable materials to be tested in line with the stresses and production processes. These include the evaluation of the edge crack sensitivity of modern, high-strength sheet materials after shear cutting using the Diabolo test developed at the Institute of Forming Technology.
Furthermore, extended testing of the bendability of sheet metal is possible with the buckling bending test. This test enables the testing of sheet metal, cast and extruded specimens with an in-situ recording of the changes in shape that occur under various dynamically applied loads. The testing of multi-axial stress states in sheet metal forming with alternating stress directions, so-called non-linear strain paths, is carried out with the aid of the hexagonal stretching frame. This allows the targeted loading of sheet metal specimens on defined, non-linear strain paths until the specimen fails.
A GLEEBLE 3800c thermo-mechanical testing system is also available in this working group for characterising various other metallic materials. Numerous other testing facilities such as an upsetting plastometer with a pressing force of 1,000 kN, a hot indentation system for testing superplastic alloys (aluminium / magnesium), testing facilities for determining limit curves of sheet materials in the plane strain space.
Material Characterization
- Tensile Testing according to DIN EN ISO 6892-1 at Room Temperature (RT) and Elevated Temperatures
- Recording of Limit Forming Curves (FLCs) according to DIN EN ISO 12004 at RT and Elevated Temperatures
- Bending Tests
- Compression Tests
- Fundamental Investigations for Characterizing Sheet Metal Materials
- Heating Trials / Microstructural Changes / Microhardness Measurements
- Pre-Straining of Sheet Samples (Applying Bi-Axial, Uni-Axial, and Plane-Strain Pre-Strains Using 6-Axis Strain Frames and Marciniak Method) / Multi-Step Testing Techniques
- Determination of Edge Crack Sensitivity
- Testing of Stainless Sheet Materials / Austenitic and Ferritic Alloys
- Modeling / Flow Curve Approximation / Flow Localization
- Construction of Testing Facilities for Bulk and Sheet Metal Forming
- Measuring / Characterizing Material and Microstructural Changes in the Customer’s Process Chain
Downloads
Information according to §5 TMG:
TGZ/TGU designation
Nobelstraße 15
70569 Stuttgart
Germany
Responsible for content in terms of press law according to § 55 RStV and represented by:
Univ.-Prof. Dr.-Ing. Dr. h. c. Mathias Liewald MBA
Register entry & VAT ID:
Stuttgart Local Court HRB 19455
Tax number 99039/02378
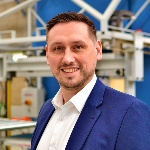
Sergei Senn
Dr.-Ing.Head of FormingLab